Brandon Talkmitt, fundador e proprietário da BTI Gauges, comentou em entrevista que a impressora 3D FUSE 1, com recurso de sinterização a laser seletiva (SLS), fez com que a empresa conquistasse um nicho do mercado, não antes explorado, como também conseguiu transformar um empreendimento paralelo em um negócio bem-sucedido em tempo integral que resistiu à pandemia do COVID-19, problemas globais da cadeia de suprimentos e aumento dos preços das matérias-primas.
FUSE 1 atendendo a demanda do nicho automobilístico da BTI Gauges
Como muitas empresas de sucesso, a BTI Gauges começou com uma lacuna no mercado – a Talkmitt estava procurando uma abordagem personalizável para a exibição de telemetria para seu carro de alto desempenho. Em um veículo típico de passageiros, as exibições do painel são limitadas a métricas padrão, como velocidade e rotações das rodas por minuto (RPM). No entanto, para carros de alto desempenho, os motoristas precisam saber muito mais sobre o desempenho do carro para navegar com segurança em velocidades acima de 150 mph. Com velocidade e potência tão altas, coisas como a pressão do refrigerante são de vital importância para a segurança. Para exibir todas essas informações, os motoristas adicionam uma série de medidores que mostram medições extras, como relação ar/combustível, aumento de carga do turbo, pressão do líquido de arrefecimento e muito mais.
“Com a energia que esses carros estão gerando, quando as coisas vão mal, elas vão mal rapidamente e são extremamente caras para consertar”, diz Talkmitt. Para evitar que as coisas piorem, os motoristas precisam ficar de olho nos monitores para evitar que o motor fique superpressurizado ou muito quente. Mas com tantas métricas diferentes para monitorar, os medidores proliferam, bagunçando a frente do carro.
Talkmitt procurou, sem sucesso, por um medidor que continha várias métricas de desempenho, para que seu pára-brisa não estivesse cheio de várias telas e leituras distrativas. Assim, como nas histórias de origem de tantos fundadores, ele simplesmente criou o que não encontrou no mercado. “Eu estava procurando por algo e ninguém conseguiu, então projetei um único medidor redondo com uma tela sensível ao toque que mostrava todas essas informações”, disse Talkmitt. Ele começou prototipando os invólucros externos dos medidores em uma impressora 3D de modelagem de deposição fundida (FDM) e testando-os ele mesmo, submetendo os invólucros a ambientes de alto calor dentro de carros e fornos e modificando o design para complementar vários modelos de carros.
Imediatamente, houve interesse em seu produto por parte da clientela que dirigia carros de corrida japoneses dos anos 90, Lamborghinis, Dodge Vipers e outros veículos de alto desempenho. Para os entusiastas que se apaixonam pela aparência de um carro, é doloroso encher um painel de instrumentos com vários medidores desagradáveis - uma leitura elegante na tela de toque único foi eficiente e esteticamente agradável.
Em um dado ponto do processo a Talkmitt encontrou outro problema. O acabamento da superfície das peças impressas em FDM não combinava com a aparência e a sensação de ponta do design do medidor. “Nem todo mundo gostou das linhas de camada”, diz Talkmitt. “Tivemos que lixar as linhas de camada e depois usar massa automotiva para preenchê-las. Foi um processo muito árduo.”
Brandon Talkmitt e a FUSE 1
A Talkmitt começou a avaliar outras opções de impressão 3D, incluindo impressoras 3D caras de fusão em leito de pó de plástico, impressoras 3D de resina e uma opção SLS compacta e barata. Mas entre os preços de meio milhão de dólares de alguns e o complexo processo de compra de materiais de outros, simplesmente não havia opções disponíveis.
FUSE 1 impressora 3D SLS
Talkmitt é apresentado à impressão 3D da FUSE 1. “Quando peguei a amostra, pensei: ‘Cara, se minhas peças podem ficar assim.’ Então fiz alguns testes, descobri que tipo de calor ele poderia tolerar. Fiz o processo de acabamento e pintura e deu tudo certo”, conta Talkmitt.
Talkmitt precisava de mais do que apenas boa aparência para aumentar a produção com o Fuse 1 – ele precisava que as peças fossem consistentemente precisas mesmo em grandes volumes e finalmente tinha uma impressora capaz de atingir tolerâncias repetíveis e apertadas. Talkmitt foi capaz de discar a precisão de seus arquivos, confiante no conhecimento de que o Fuse 1 poderia imprimir com precisão os recursos detalhados que ele projetou.
“Eu desenhei um furo de 40 mm x 40 mm, e agora com o Fuse 1 posso imprimir um 40 x 40 pinos, e vai caber. Fazemos roscas e outros recursos que precisam ser precisos. Em um ambiente automotivo, outras partes se deformariam, mas desde que mudamos para o Fuse 1 não tivemos uma parte deformada”
Brandon Talkmitt
FUSE 1 Vantagem de ter uma impressora SLS
Para BTI Gauges, conseguir algo que o autor Nassim Nicholas Taleb considerou, ‘Antifragilidade’. Entidades antifrágeis são aquelas que não apenas suportam pressões e choques, mas se tornam mais fortes, melhores e mais eficientes por meio deles. Durante os problemas da cadeia de suprimentos dos últimos dois anos, a BTI Gauges enfrentou várias deficiências de telas sensíveis ao toque e outros componentes necessários para suas nove linhas de produtos. Para um fabricante frágil, essa escassez pode ter interrompido a produção, distribuição e geração de receita. Para Talkmitt, eles o forçaram a fornecer novos tipos de monitores, o que afetou o tipo de processador, placa de circuito e o formato do próprio medidor.
Ao trazer a impressão 3D internamente com o Fuse 1, ele conseguiu mudar imediatamente para um novo design, sem ter que gastar milhares de dólares em novas ferramentas ou lidar com uma lista de pendências de produtos agora obsoletos. “Eu teria ficado preso com todo aquele plástico, mas com o Fuse 1, eu poderia fazer a mudança na hora. Foi uma coisa de 30 minutos para eu mudar os arquivos. Sem isso, eu definitivamente estaria preso agora”, diz Talkmitt.
A Talkmitt não dependia de um provedor de serviços externo e mantinha tudo o mais verticalmente integrado possível. Enfrentar várias carências o levou a desenvolver um inventário digital de peças de reposição para se proteger de futuras faltas na cadeia de suprimentos. Lidar com pressões econômicas fora de seu controle realmente fortaleceu seu modelo de negócios e o isolou de choques futuros – a definição de antifrágil.
Produção de alta potência
Para manter a produção contínua econômica e sustentável, a Talkmitt conta com a eficiência de todo o sistema Fuse Series. Utilizando o algoritmo de empacotamento avançado do PreForm, ele é capaz de aninhar peças dentro de outras para aumentar sua densidade geral de empacotamento e combiná-la o mais próximo possível da taxa de atualização de 30% do Nylon 12 Powder. “Um de nossos produtos é um medidor de 4,3 mm que precisa de uma peça frontal e traseira, mas há todo esse espaço no meio, então eu pego uma peça de 3,5 mm e as aninho dentro. Podemos preencher estrategicamente o volume de construção e atingir regularmente 25% de densidade de embalagem”, diz Talkmitt.
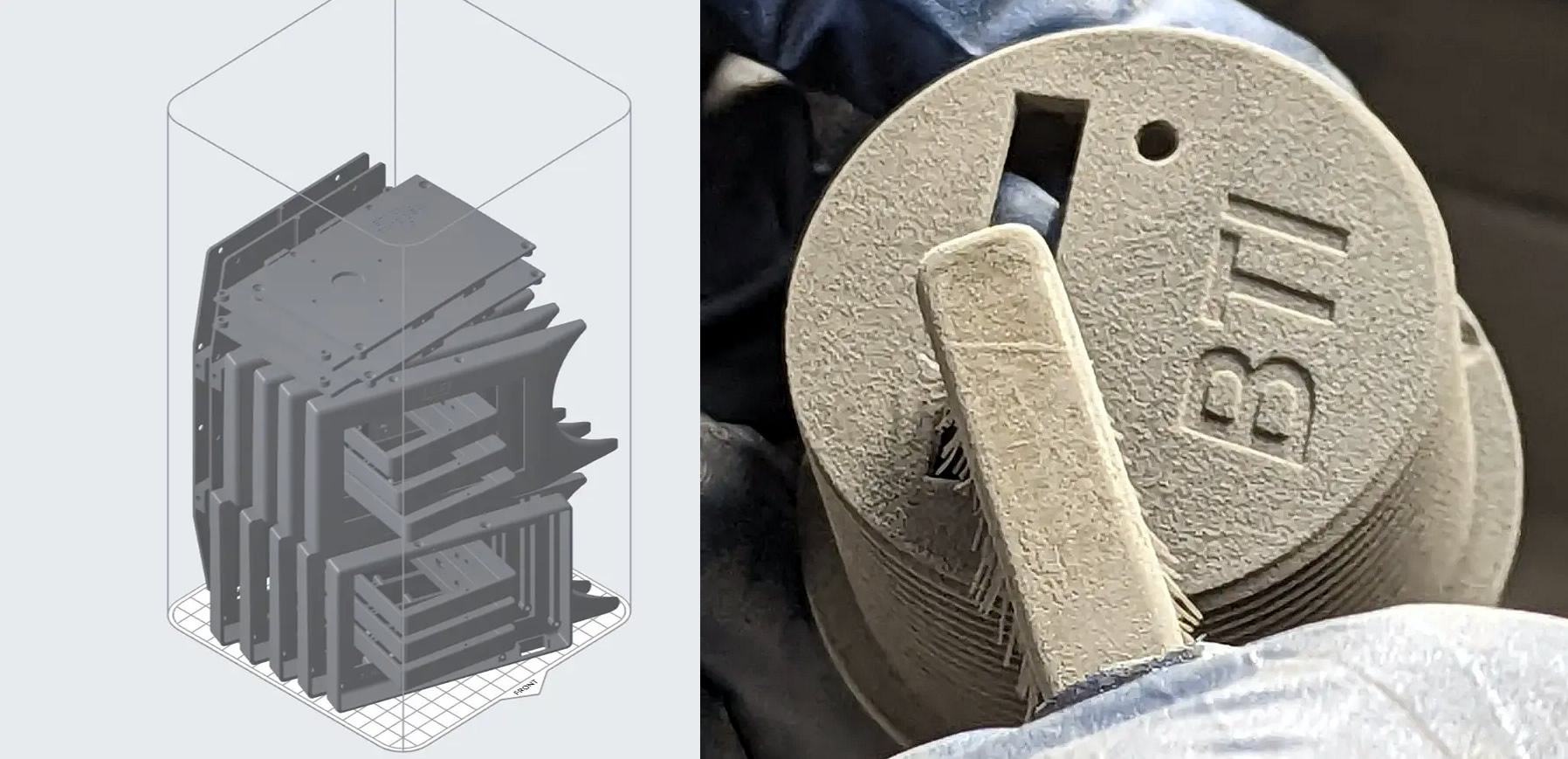
Uma câmara de construção do Fuse 1 embalada mostrada no PreForm, com peças aninhadas dentro de peças maiores (esquerda), e uma peça impressa do Fuse 1 no estágio de pós-processamento (direita).
Ao embalar de forma eficiente as peças com uma densidade tão alta, a Talkmitt pode atingir um fluxo de trabalho de impressão com desperdício quase zero , onde cada pedaço de pó é usado em sucessivas rodadas de impressão. Para um pequeno fabricante, essa eficiência cria um custo menor por peça e um prazo mais rápido para ROI positivo.
O alto rendimento do Fuse 1 permitiu à Talkmitt fazer a transição de três impressoras FDM que estavam funcionando sem parar, para uma vez por semana, câmaras de construção totalmente embaladas no Fuse 1. A utilização do fluxo de trabalho simplificado do Fuse Sift permite que a Talkmitt gaste menos tempo pós-processamento , e mais tempo para projetar novas peças e aumentar a presença da marca. “Na parede de trás da nossa loja temos o Fuse 1, Fuse Sift e o gabinete de jateamento. Em seguida, pintura, montagem e encaixotamento serpenteiam pelo chão da fábrica. O tamanho e a pegada do Fuse 1 funcionam perfeitamente para o processo”, diz Talkmitt.
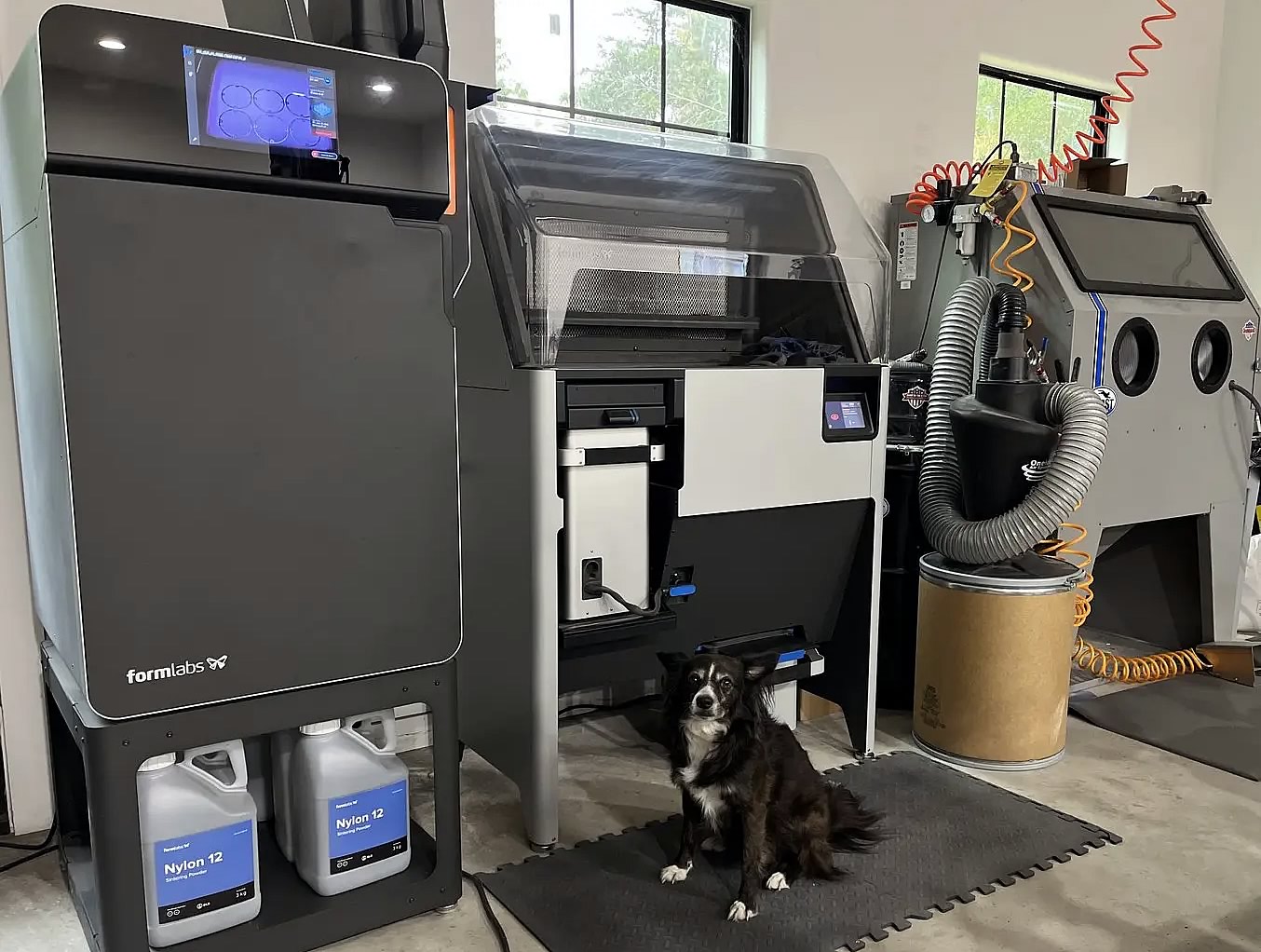
Fuse 1 e o Fuse Sift têm um espaço acessível e um fluxo de trabalho simplificado que pode caber facilmente em espaços de trabalho existentes.
Como um novo negócio, entrar em uma indústria onde os carros são vendidos rotineiramente por centenas de milhares de dólares é difícil. Fazê-lo em meio a uma paralisação global, problemas na cadeia de suprimentos internacional e turbulência econômica é quase impossível.
Ao implementar a fabricação interna com uma impressora SLS de alta qualidade como a FUSE 1, ele conseguiu controlar e proteger seu poder de produção, elevando-o acima daqueles que ainda dependem da fabricação tradicional ou de fornecedores externos. “Recomendaria a qualquer um. O Fuse 1 mudou o jogo para nós”, diz Talkmitt.
FESMO Distribuidor Ofical Formlabs Brasil
Para conhecer mais sobre a FUSE 1, preencha o formulário abaixo para maiores informações